
Industry News
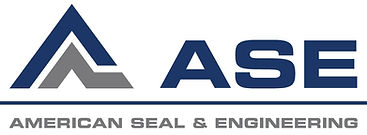

1-800-719-1869
Frequently Asked Questions
Have some questions? Take a look here to see if we have the answer. If not, contact us here.
-
What are the limits to what we make?
-
Can we make new metal seal designs to meet with specific customer needs?
-
What is the design and product development cycle for a special, complicated application?
-
How do customers utilize our sales, engineering, and manufacturing processes?
-
What is the average lead time for deliveries of products or parts?
1. What types of metal seals do we manufacture?
American Seal & Engineering manufactures metal seals. Information on specific seals can be found in our Products Page. We provide metal seals for the following: all fluids and gases; pressure ranges from vacuum to 100,000 psi; internal, external, bi-directional, and axial pressure orientations; temperature ranges from cryogenic to 1950ºF (1065ºC); leak rates greater than or equal to 10^-10 cc/sec He; and a diverse range of joint shapes, material types, and material coatings. With information about specific design envelopes or applications, our experienced Sales Engineers can help design the right product for your application. Fill out our application form to begin the process of engineering a solution that meets your requirements. If you prefer to speak directly with a Sales Engineer you may call our Sales Department at (203)789-8819 for assistance now. We are available Monday to Friday from 8 a.m. to 5 p.m. Eastern Time by telephone and are always accepting e-mails.
2. What are typical metal seal applications?
Typically, metal seals are used in applications with the following conditions; high temperature, radiation, vacuum, high pressure, corrosive, or toxic environments where the media being contained is either a fluid or a gas. We will provide you with the metal seals specific to your needs once we receive details on your application. You can fill out our application form, call, or email us directly.
3. What are the limits to what we make?
You tell us what obstacles you need to overcome and we will work to find a solution. Each metal seal has unique characteristics and properties. The application determines what type of seal is engineered, what media is to be sealed, temperature, pressure, etc., and all have influence on the selection of a seal that will meet with performance criteria. We have a large product portfolio and the ability to customize an existing product or develop a new seal design in our effort to provide the right solution for your application. Contact our Sales Department directly to discuss your requirements.
4. Can we make new metal seal designs to meet with specific customer needs?
Yes. As long as we have all the application and performance requirements, our Sales Engineers, in cooperation with our Engineering department, will design a metal seal to meet with your specifications. Our Sales Engineers will interface with your design team during the entire process. Once a design is complete our technical team will provide complete product drawings and performance expectations for your review and approval.
5. What is the design and product development cycle for a special, complicated application?
We have the shortest product development cycle in our industry. We ask the customer to provide our sales engineer with a complete description of the application. This includes drawings, sketches, the status and advancement of the program, etc.. Our technical team then reviews this data and prepares for a Phase 1 technical-review meeting with the customer.
Following the Phase 1 technical-review meeting, our technical team finalizes our recommended design and forwards the technical data to the customer for review. It is then the customer’s responsibility to review our seal design and confirm that all specifications meet their requirements.
Following the customer review and approval, we then provide a formal quotation, including lead time for development and production hardware. Upon customer acceptance, the product is released for initial pre-production.
6. How do new customers utilize our sales, engineering, and manufacturing processes?
A metal seal design project typically starts with an application review. It takes place at the customer’s facility or is conducted through a conference call or Web meeting between an American Seal & Engineering Sales Engineer and the customer’s design or project Engineer. After the initial project review, one of our Sales Engineers will present a design proposal with one or multiple design options. The design options are then presented to the customer with a description of the seal or sealing system together with the recommended mating hardware configuration, complete with tolerances for evaluation and critique by the customer. After the customer’s approval of the proposed sealing concept, we then prepare a formal quotation or proposal typically within 24-48 hours that includes a detailed description of the recommended product, price, and delivery of the product, and if applicable, tooling or gauging.
7. What is the average lead time for deliveries of products or parts?
American Seal & Engineering is committed to having the shortest lead-times in the industry. Lead times vary depending on the type and complexity of the seal or sealing system being proposed. Our average on-time delivery percentage in the last five years is over 92%, , which means we don’t just quote the shortest lead-times in the industry, we deliver on our commitments.