
Industry News
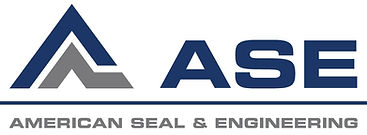

1-800-719-1869

Pressure fluctuations and heat are constant concerns for designers of aircraft engines, valves, pressure transducers, exhaust manifolds, and fuel injectors. A combination of these two factors can result in premature failures or short seal life. AmeriSeal™ C-seals help overcome both heat and pressure pulsating sealing problems. The key to the seal's performance is the high spring back characteristic due to the C-shaped construction. These highly resilient seals can be used for internal, external, and axial pressures under extreme conditions that preclude the use of gaskets made of organic materials. This uniquely fabricated seal configuration is capable of producing relatively high levels of spring back. The compression of the seal in a controlled groove or between two radial interfaces produces a counter load, generating an effective sealing action that is ideal for these special applications.
AmeriSeal™ C-seals will undergo plastic deformation when installed at the 20% recommended compression. These C-seals may be reusable in their original cavities or in cavities that are nearly the same depth as the original.
C-ring seals have much lower initial flange load requirements than O-rings. However, it is still high enough to provide effective smearing of the plating or coating used on sealing surfaces. Deflection capability is excellent and it is normally assumed to be about half of the spring back; however, this is a function of the operating conditions and the required leakage rate.
In the seal selection process, the designer should always keep in mind basic design criteria. There is a direct relationship between seal OD and the seal free height. Larger free heights provide better resilience and the performance tends to be more consistent.
Seal selection is a process of optimizing design capabilities and managing design limitations such as size, available load, spring back, performance requirements, and cost.
The most important factors in C-ring seal design are:
Maximum pressure and direction
Extreme operating temperature
Allowable leakage rate
Available flange load
Internal Pressure
External Pressure
Axial or Radial Pressure
Deflection Capability:
We define capability by the seal’s ability to continue to seal as the flanges separate under pressure. This function is related to free height, material type, material heat treatment, and diameter. In most circumstances, the larger the free height of the seal, the more resilient the seal will be. More resilient seals allow for greater flange separation and more liberal manufacturing tolerances of the flanges which need to be flat and parallel.
AmeriSeal™ C-Ring Seals Material Types:
AmeriSeal™ C-ring Seals can be made of almost any alloy that can be formed. However, because strength and temperature properties are the primary technical consideration, we produce our AmeriSeal™ seals primarily from high temperature super alloys.
AmeriSeal™ C-Ring Seals Plating and Coatings:
Where very low leak rates are demanded, C-rings are plated or coated to provide a relatively soft surface which flow into the minor imperfections of the flanges at installation. Plating or coatings will not compensate for poor surface finishes on the mating hardware. The selection of plating or coating is based on the allowable leak rate, the density of the fluid, flange roughness, and the application temperature.
C-Seals

